Machine Learning accelerates the simulation design process
Written by Marco Turchetto and Alessandro Viola
20 April 2021 · 5 min read
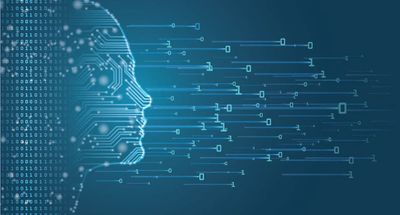
Machine Learning (ML) is a branch of Artificial Intelligence that permeates our everyday life: from the moment we wake up in the morning to the moment we go to bed at night. It is the engine that powers many online services we use and that influences our behaviors learning from our past experiences. The idea behind this is that systems can learn from data, identify patterns on their own and make decisions with minimal human intervention.
The same applies to engineering and CAE-based product design where ML provides a real benefit to simulation-based computer experiments. There are some challenges that engineers have to deal with when performing simulation analysis where ML can be of real help:
- Long simulation time due to the size of the physical engineering problem
- Availability of external CAD/CAE solver licenses
- Expensive hardware to run simulations
ML can be the solution to reduce the simulation turnaround time, minimize solver runs, make smarter use of computing resources, and speed up the whole simulation design process. In addition, ML can be exploited effectively in simulation when performing RSM design space exploration.
Response Surface Models (RSM) are mathematical and statistical tools that approximate, analyze and simulate complex real-world systems. RSM allows getting an instant and accurate insight into the relationship between a set of parameters and one or more design objectives when a simulation based on real-physics models is not affordable in terms of computational time.
For example, RSM ML-assisted algorithms can bring the added value to fully exploit the historical and experimental datasets to quickly build and train an effective meta-model, validate its accuracy and use it to perform an additional RSM-based optimization.
However, building a useful and representative RSM is not a trivial task for many reasons starting from the RSM training to its validation.
ML assisted alghorithms exploit your simulation and experimental datasets to build and train an effective metamodel, and use it for RSM-based optimization.
ML in Design Space Exploration
At ESTECO, ML is part of our design exploration and optimization technology. modeFRONTIER, our software solution for process automation and design optimization, employs ML methods to:
- Build surrogate models on the top of corporate datasets and make them available to support the exploration of possible good solutions,
- Empower self-adaptive exploration algorithms to explore the design space by improving their internal knowledge step by step at runtime, with limited input from the engineer.

Our RSM technology generates reliable metamodels that are effective in approximating the multivariate input/output behavior of complex systems with no computational effort. The training, validation, and screening tools help create the most accurate model choosing from a wide range of methods. By evaluating the accuracy indicators, comparing surfaces, and contextually understanding variable correlations, experts can focus on RSM tuning while the entire team benefits from model re-use. Our comprehensive suite of RSM algorithms include ML methods, like Support Vector Machines (libSVM), H2O.ai, and Neural Networks.
After exploring and understanding relations underlying the Design Space, engineers can access a wide selection of intelligent algorithms, available in modeFRONTIER, to further refine their designs and identify optimal candidate solutions. The suite of our optimization algorithms tackle both discrete and continuous variables to solve single and multi-objective problems. pilOPT, one of our proprietary algorithms, includes different internal optimization strategies which exploit ML logic to perform a smart exploration of the design space. It combines the advantages of local and global search, and balances in an intelligent way the real and RSM-based (virtual) optimization in the search for the Pareto front.
With pilOPT, you can expect to:
- Set up an initial investigation of the design space
- Identify promising areas of the design space to further exploit
- Address both multi-objective and single-objective optimization problems, and reach the optimum after few design evaluations
- Run it also in autonomous mode (no parameters set-up needed) and automatically find the number of designs needed to reach the Pareto frontier and explore it properly, even in the computational heavy cases
Train RSM with ML algorithms: a time-saving good practice for combustion engine process optimization
If you look at a common automotive engineering problem as optimizing engine emission levels, there are many different complex physical and chemical phenomena involved during the engine combustion process. The simulation of these events not only requires expertise, but also high computing resources and long analysis time. This makes extensive design space exploration studies often unfeasible to perform.
Typically, in this scenario, you have to play with many different input factors like the compression ratio, the fuel injection timing, valve timing, and many other parameters in order to maximize the power output of the engine while minimizing its fuel consumption and emissions. The use of ML to train high-quality RSMs can be the solution to effectively interpret the behavior of the engine and achieve accurate predictions.
Indeed, combining experimental and simulation data with ML algorithms, available in software solutions as modeFRONTIER, enables you to reconstruct the physical behavior of the engine. When the RSM (as the output of ML algorithm) is available and its quality assessed, you can use this metamodel to perform RSM-based design space exploration which does not require a huge amount of simulation time. This is where RSMs come help to speed up the exploration and optimization process. The real heavy and long-time simulation model is used just to verify the validity of the solution found with the metamodels.
Democratize ML in the context of the Simulation Process and Data Management (SPDM) platform
Once your ML-trained metamodel is tuned to get the best performances, and this is probably the most complex task, it is also important to exploit it at the most. Here comes the so-called democratization in simulation. It means making this metamodel profitable not only for simulation experts but also accessible and usable to everyone in the company, even if you are not necessarily an ML expert.
In fact, with VOLTA, a collaborative platform for Simulation Data and Process Management (SPDM) and Design Optimization, you can fully capitalize ML domain expert’s abilities. This means making the best metamodels accessible to a broader audience, enabling other actors, involved in the simulation design process, to perform further analysis or take informed decisions.
All this comes with all VOLTA SPDM capabilities, bringing key advantages:
- Intellectual property retention: the creator of the Metamodel is registered and traced
- Full traceability of data generated with the metamodel to understand who produced the design data and which model has been used
- Guided Multidisciplinary Design Optimization (MDO) workflows: interchange selected time demanding Single Discipline Optimization (SDO) models with the inexpensive ML-trained metamodel to speed up the overall MDO process
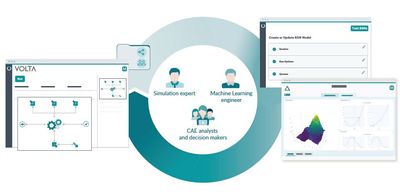
Overall, ML incorporated in ESTECO Technology empowers your RSM-based optimization studies when the complexity of a physical engineering project could require huge simulation time and computation costs. Also, by bringing ML in the context of the SPDM platform as VOLTA, you can expect to scale up the usage of metamodels across teams and different organizations to speed up the simulation process and design better products, faster.
VOLTA is the enterprise platform for Simulation Process and Data Management, and Design Optimization
Take full control of the engineering design process
VOLTA is the enterprise platform for Simulation Process and Data Management, and Design Optimization
Take full control of the engineering design process
VOLTA is the enterprise platform for Simulation Process and Data Management, and Design Optimization