Streamline eVTOL aircraft propeller design with a server-based framework for MDAO studies
Written by Alexander Duggan and Vivek Ahuja
15 February 2023 · 10 min read

In the design of any complex system, design optimization is a key activity to improve product performance, meet various stakeholder requirements, and reduce cost and time to market. In the automated search of the design space, design optimization makes extensive use of computer-aided-engineering (CAE) simulations. Engineered systems combine sub-systems and components; each part is modeled by different physics and the performance assessment covers a range of engineering disciplines including: fluid-dynamics, structural, thermal, electro-magnetic, and many others. This combination is termed multi-disciplinary design analysis and optimization (MDAO). The motivation for using an MDAO framework is to have a proven method in place that can meet the demands of a changing and increasingly complex environment.
Why Multi-disciplinary Design Analysis and Optimization (MDAO) for eVTOL aircraft development
Over the last decade the emerging prevalence of Distributed Electric Propulsion (DEP) in aviation has added a new paradigm to the aircraft design problem. Electric Vertical Take-off and Landing (eVTOL) aircraft work within a uniquely constrained multi-disciplinary environment. The propellers for this genre of aircraft must operate in cruise as well as in vertical and transitional flight modes. Some designs augment flow using a collection of electric motor-driven high-lift propellers (HLP) for lift augmentation in low-speed flight conditions, while other designs can provide additional thrust for vertical or short takeoff and landing (V/STOL). Several concepts aim to realize favorable interactions between the airframe aerodynamics and strategically integrated propulsors, achieving hitherto unrealizable performance benefits. These propellers must be structurally sound to deal with complex vehicle transitions. They must be quiet to allow vehicle operation in densely populated urban environments in order to accomplish Urban Air Mobility (UAM) tasks.
FlightStream® aerodynamic modeling solver meets computational efficiency for MDAO aircraft studies
Early design exercises require tools having both high computational efficiency and sufficient fidelity to reliably guide the development of vehicle concepts. However, the same highly coupled aero-propulsive interactions are difficult to model with sufficient levels of accuracy in early design stages (conceptual and preliminary). Commercial and open-source low- and mid-fidelity tools implementing vortex lattice methods, surface vorticity methods, seeded particle methods, or lifting line theory have emerged to fill this capability gap.
FlightStream® is a surface vorticity solver which provides reliable analysis of aerodynamic loads while maintaining computational efficiency levels required by most MDAO pipelines
By using reliable, efficient tools in the earlier phases of design, more mature designs emerge early in the design process. While Computational Fluid Dynamics (CFD) tools which solve the unabridged continuum Navier-Stokes Equations provide the necessary fidelity to refine designs they generally lack the computational efficiency to sufficiently inform early design.
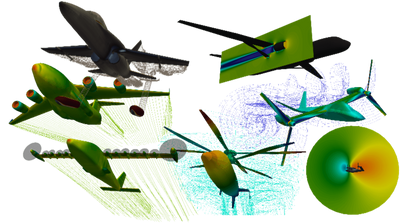
Flightstream allows for rapid analysis of unconventional aircraft using a unique surface vorticity, flow-separation and viscous analysis capability for both powered and unpowered configuration.
FlightStream® is a surface vorticity solver which provides reliable analysis of aerodynamic loads while maintaining computational efficiency levels required by most MDAO pipelines. The solver uses vorticity sheets to provide solutions in minutes. This solver has also been coupled with an aeroacoustics capability to allow the modeling of noise in early design stages.
ESTECO VOLTA SPDM platform facilitates MDAO studies for eVTOL propeller performance improvements
We partnered with Research in Flight to showcase a methodology for optimizing an eVTOL propeller geometry to meet stakeholders’ competing requirements and key performance metrics. Commonly such a complex task would be too time-consuming and costly to solve. Especially when high-fidelity volume-based Computational Fluid Dynamics (CFD) becomes the bottleneck.
We addressed this design challenge by combining ESTECO VOLTA SPDM platform and its MDAO capabilities with the FlightStream® aerodynamic analysis tool. The physics are captured by incorporating multiple analysis and disciplines.
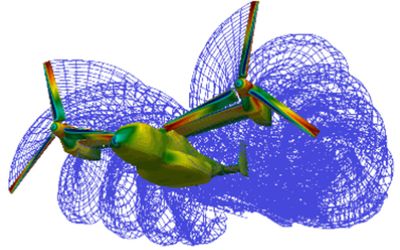
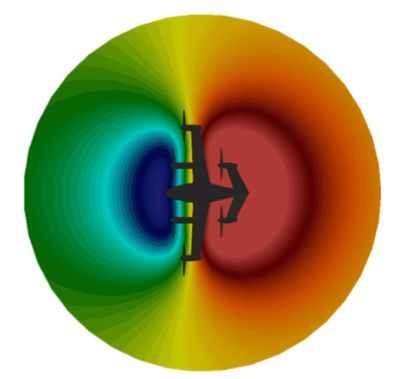
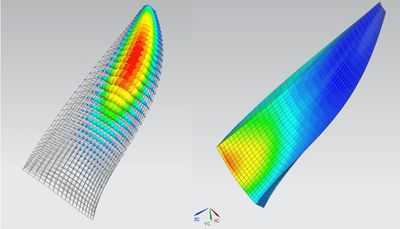
Aero-propulsion (FlightStream), Aero-acoustics (FlightStream) and Structure (NX Nastran) analysis
In particular, the eVTOL propeller was geometrically modeled using Bernstein polynomials feeding cross-sectional data of the propeller to the FlightStream Component Cross-Section (CCS) file format. The CCS file [4-6], is a text file that allows the user to import aircraft geometry into FlightStream in a manner suitable for automatic mesh generation. The CCS file also allows the user to define control surfaces and set several meshing options. For this work, a FORTRAN script was written to automatically convert the Bernstein polynomial data into sectional cross-section data for the CCS file format. The process by which this geometry is conceived and the means by which it is built are crucial aspects to the development of the optimization formulation. The process by which the geometry is constructed should be accurate and replicable. Furthermore, the design space should not be limited by the design tool used to create the geometry.
Then these parameterized models for aero-propulsion, aero-acoustics, and stress analyses were automated into the ESTECO modeFRONTIER modular MDAO workflow and published on VOLTA SPDM platform ready to be executed.
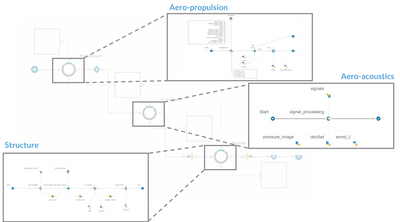
VOLTA SPDM platform leverage ESTECO’s modeFRONTIER simulation process automation workflow
This workflow enabled an optimization framework for eVTOL propellers with the goal of satisfying four discipline related objectives. In terms of aero-propulsion discipline, we were interested in maximizing the thrust while minimizing the torque of the propeller. From the acoustics discipline, the goal is to be as quiet as possible, so we were interested in minimizing the sound pressure level. Finally, we included a Finite Element Analysis (FEA) discipline where we wanted to minimize the propeller mass and make sure that our stresses were within allowable limits and therefore meeting requirements.
We used the ESTECO proprietary pilOPT algorithm to find an optimal geometry for the eVTOL propeller with the best tradeoff between the objectives listed above. The proprietary pilOPT algorithm is one of our most advanced optimization strategies. It self-adapts to your design problem; adjusting strategies on the fly as required to get you a pareto frontier with tradeoff space coverage in a reasonable amount of time.
Once the MDAO workflow has been set up, it is published on the ESTECO VOLTA enterprise platform to be executed. Thanks to its web interface and the collaborative environment for SPDM, VOLTA speeds up the communications among the subject matter experts and the stakeholders. The framework also enforces standardization and the formalization of simulation and business processes as an institutionalized method, promotes knowledge reuse, and facilitates the sharing of needed resources.
Through VOLTA Data Manager, subject matter experts can store, version and share their CAD/CAE models and MDAO workflows securely in a web environment
In VOLTA, each subject matter expert (SME) owns and is responsible for maintaining their part of the overall MDAO study:
- The CAD expert generates the geometry of the blades providing a parametric model and the CAD solution used to vary the propeller’s shape.
- The aerodynamic expert sets up the aerodynamic simulation model, which uses the geometry model to evaluate its aerodynamic performance using FlightStream®, and makes it available to the structure expert to impose aerodynamic loads on the blade.
- The acoustics expert also uses the output of the aerodynamic simulation to calculate sound pressure levels at various observer positions.
- The simulation expert concates all those models into the automated MDAO workflow to be easily executed from a web interface and re-used for further analysis.
Next step was to add a Plan to the MDAO workflow from the VOLTA web interface. This allowed the simulation expert to submit the MDAO study to optimize the propeller shape to increase performance while meeting all design requirements.
With VOLTA Planner, subject matter expert can execute MDAO workflows from an intuitive web interface
A Plan means adding some types of design space exploration studies. It can be a Design of Experiments (DOE) or an optimization routine analysis. Through the VOLTA Planner interface, everyone involved in the project can change requirements, performance metrics, input domains and design space exploration strategies. And you can have many different plans built on top of the same MDAO workflow.
From the process execution side, while the CAD solver and the internal code can easily run-on local resources, the aerodynamic simulation may require additional computational resources and software licenses. ESTECO state-of-the-art job scheduling technology allows organizations and teams to take full advantage of current on-demand cloud computing services such as Amazon EC2 or other public, private and hybrid cloud preserving the protection of the exchanged data through the use of virtual private networks and secure communications protocols to solve MDAO at scale.
Finally, stakeholders interested in the results of the optimizations can easily access and select the best propeller shape designs via the VOLTA Advisor web dashboard.
VOLTA Advisor enables subject matter experts to create web-based post-processing dashboards for analyzing MDAO studies
The VOLTA Advisor acts like the Authoritative Source Of Truth (ASOT) for trade space studies on the web. In this way, design stakeholders can log in, view the same data as all other stakeholders, apply their preferences, requirements, and performance goals. In this case, the performance goals would be sound/noise levels, thrust and torque of the propeller design, along with ensuring stress requirements are met. After these filters are applied to the data, they could make tradeoff decisions quicker and in a collaborative way rather than copy data and static images into powerpoints which are shared via email with no traceability at all.
Watch this webinar on MDAO studies to learn more how ESTECO's efficient server-based approach to MDAO combined with Research in Flight's aerodynamic analysis tools enable organizations to optimize eVTOL aircraft propeller design in a fraction of time.
Dr. Vivek Ahuja is the CEO and co-founder of Research in Flight, the developer of FlightStream. He holds a PhD in Aerospace Engineering from Auburn University. Dr. Ahuja’s work over the past decade has focused on theoretical and numerical subsonic aerodynamics, with an emphasis towards surface vorticity and its applications to attached and separated flows. Dr. Ahuja has developed many innovations with surface vorticity for high-lift flow and has been in charge of commercializing the FlightStream flow solver for the aerospace industry worldwide. He has authored many technical papers on these topics at conferences and in journals. Dr. Ahuja has held software development positions in the CFD industry and served as the principal investigator on several NASA, DoD and USAF SBIR programs.
Dr. Vivek Ahuja is the CEO and co-founder of Research in Flight, the developer of FlightStream. He holds a PhD in Aerospace Engineering from Auburn University. Dr. Ahuja’s work over the past decade has focused on theoretical and numerical subsonic aerodynamics, with an emphasis towards surface vorticity and its applications to attached and separated flows. Dr. Ahuja has developed many innovations with surface vorticity for high-lift flow and has been in charge of commercializing the FlightStream flow solver for the aerospace industry worldwide. He has authored many technical papers on these topics at conferences and in journals. Dr. Ahuja has held software development positions in the CFD industry and served as the principal investigator on several NASA, DoD and USAF SBIR programs.
ESTECO's efficient server-based approach to MDAO combined with Research In Flight's aerodynamic analysis tools enable organizations to optimize eVTOL aircraft propeller design.
Solve complex MDAO aircraft studies in a fraction of the time
ESTECO's efficient server-based approach to MDAO combined with Research In Flight's aerodynamic analysis tools enable organizations to optimize eVTOL aircraft propeller design.
Solve complex MDAO aircraft studies in a fraction of the time
ESTECO's efficient server-based approach to MDAO combined with Research In Flight's aerodynamic analysis tools enable organizations to optimize eVTOL aircraft propeller design.