Instant design predictions with Explainable AI through Reduced Order Modeling
Written by Simone Genovese and Angela Scardigli
23 January 2024 · 10 min read
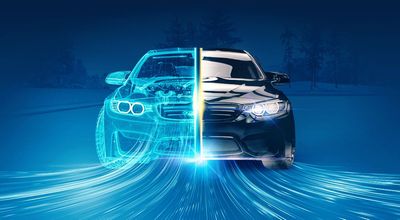
In the globally competitive landscape of today’s manufacturing industry, companies are under constant pressure to innovate while keeping costs low. To successfully overcome these challenges, they rely heavily on CAD/CAE software which essentially replaces the need for physical prototypes, providing a much more efficient and cost-effective way to get performance insights early in the design process. Although high-fidelity CAE simulations offer many advantages over experimental methods, interpreting and applying the data they produce typically requires a high level of expertise. Consequently, simulation results remain confined to a few experts within silos, preventing them from being used in other steps of the design process.
Additionally, physics-based simulations, such as Computational Fluid Dynamics (CFD), require a lot of computational power, memory, and storage. This can be a considerable barrier for many companies, particularly smaller ones, as it necessitates access to high-performance computing systems and can result in substantial operational costs. Because of these resource constraints, the use of CFD is typically restricted to the design cycle and pre-production phases. For example, in the automotive industry, it is often used as a more cost-effective alternative to wind tunnel vehicle aerodynamics testing, which can be a significantly more expensive and time-consuming process.
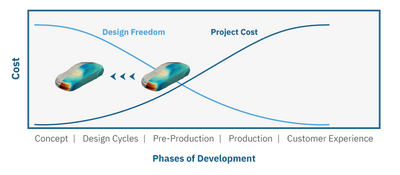
Today, Original Equipment Manufacturers (OEMs) need accurate, high-fidelity data as soon as possible to shorten product development cycles. The ideal scenario would involve employing CFD evaluations during the conceptual design phase itself. By using these advanced simulations at this early stage, suppliers could provide the high-fidelity data that OEMs require with the lowest cost investigation. This would allow for a more precise understanding of how a product performs under various conditions, leading to more effective and efficient design decisions before moving into more expensive stages of product development.
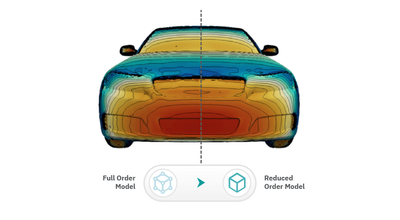
Combine physics-based through data-driven modeling
Real-life applications are complex and using physics-based simulation methods to investigate them is computationally expensive and time-consuming. There's an increasing trend towards leveraging existing simulation data to train simplified mathematical models with Machine Learning (ML) techniques to address these challenges.
Reduced Order Modeling in particular offers a powerful approach to deal with complex, high-dimensional problems that are typically associated with 3D CAE simulations. It reduces the complexity of a full-order numerical model while preserving its essential behavior. Reduced Order Models (ROMs) with respect to standard Response Surface Models (RSM) are surrogate of the whole solution, you don’t just get some quantity of interest, but you really obtain a comprehensive model of your problem. They represent a low-cost surrogate for the full-order model, but still encapsulate the relevant core features and behaviors of the original problem. This permits the quasi real-time evaluation of complex physical phenomena, exploiting the information provided by a carefully selected space of design solutions.
By using ROMs, engineers can:
- Perform real-time or quasi real-time simulation analysis.
- Obtain a surrogate of the whole CAE solution, not just some quantity of interest.
- Preserve space resolution of the full-order model: same physics/hypothesis.
- Analyze physical phenomena such as flow separation, turbulence and cavitation.
- Explore new scenarios for design optimization and uncertainty quantification.
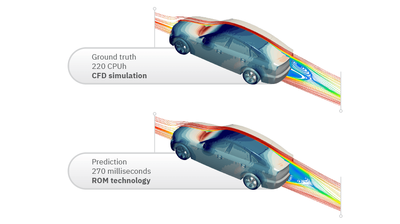
In essence, machine learning methods coupled with ROMs provide a pragmatic solution to the challenges posed by the high computational demands of full-scale 3D CAE simulations. By enabling the construction of accurate, less resource-intensive surrogate models, ROMs allow for quicker, more cost-effective analyses in the field of CAE. This not only facilitates rapid iterations and quicker decision-making during the design process, but also enables fast and accurate predictions during the conceptual design phase.
romBOX: Explainable AI for Reduced Order Modeling
At ESTECO, we are partnered with Optimad, a pioneering service provider in the field of scientific computing, to bring advanced ML and Explainable Artificial Intelligence (XAI) capabilities into the modeFRONTIER and VOLTA software solutions. Optimad has transferred its expertise in XAI and ROMs for numerical simulation into their romBOX software.
RomBOX is a Reduced Order Modeling and ML toolbox designed to perform data-driven model reduction for parameterized design problems. It employs a non-intrusive mathematical technique called Proper Orthogonal Decomposition (POD) to encode the solution space and reduce its dimensionality. Also known as Principal Component Analysis (PCA) and Singular Value Decomposition (SVD), the POD has gained relevance in many engineering applications, due to its optimal compression rate: in fluid dynamics, particularly, it has been often used for the analysis of turbulent flows, since it is capable to identify relevant flow field structures starting from a collection of solutions.
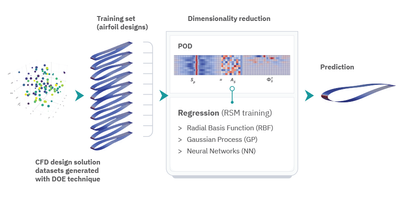
Consider a common fluid dynamic problem, like the analysis of the flow field past airfoils with different shapes. Given a database of CFD solutions corresponding to different airfoil designs, it’s possible to build a training set to compute a POD basis and extract all the relevant information contained in the solution data. The training set solutions, e.g. the pressure field over each airfoil, are rearranged into a matrix (each matrix row-wise picture can be interpreted as the unrolled airfoil surface mesh) that can be expressed through POD as a linear combination of coefficients and POD modes. The modes are ordered in terms of their energy contribution, from largest to smallest, meaning that the first ones capture the majority of the energy contained in the dataset and contribute the most to its approximation. By truncating the basis, it is possible to obtain a more concise representation of the information contained in the original dataset. Once a parameterization is given or derived a-posteriori through geometry encoders, the relevant coefficients of the POD expansion for new designs can be determined by training regression models, based on:
- Radial Basis Functions (RBF), very quick to train and suited for high-dimensional spaces.
- Gaussian Processes (GP), capable of handling noisy or limited data, and predict intricate patterns.
- Neural Networks (NN), suitable for capturing highly non-linear relationships between inputs and outputs and dealing with large and complex datasets.
Consequently, the corresponding flow solution is retrieved by linearly combining the POD modes.
Non intrusive data-driven methods such as ROMs represent a valuable asset for CAE engineers who don’t have at their disposal the necessary hardware resources, like huge Graphics Processing Unit (GPU) clusters, to train computational-intensive deep learning models on large datasets. ROMs can be trained on standard CPU architectures, are easily and efficiently parallelized and, given their compression quality, can be effectively used to limit data storage space.
Moreover, ROMs leverage prior knowledge and physics-based principles to model the data. This is why they work so well with relatively small datasets compared to deep learning approaches, that commonly require a lot of data to infer the relationship between the inputs and the outputs. And Reduced Order Modeling techniques provide you with interpretable results, enabling XAI by making it easier to understand the relationships between variables and the physical or engineering principles underlying the model. Compared to deep neural networks which can be challenging to interpret, making it difficult to understand how and why they arrive at certain predictions, ROMs are easier to interpret and allow one for a clearer understanding of the reasoning behind predictions.
Build CAE datasets and automate ROM training with modeFRONTIER
Optimad’s romBOX toolbox is fully integrated with modeFRONTIER, our intuitive vendor -agnostic solution for process automation and design optimization. The first step in training ROMs is to build your CAE datasets with modeFRONTIER. By integrating a third-party CFD solver into the simulation workflow, you can apply Design Of Experiments (DOE) algorithms to generate a small training set of designs that explore the entire space of input variables like the angle of attack of the airfoil and its shape for aircraft aerodynamic assessment.
The CFD solver embedded in the modeFRONTIER workflow enables you to compute the pressure field on the airfoil surface mesh for each configuration of the DOE. At the end of this phase, you can analyze your airfoil design datasets by extracting the ROM model with the romBOX node integrated in the modeFRONTIER workflow. Once you get the trained reduced order model, you can execute ROM-based fluid dynamic analysis by providing geometrical input parameters to predict the pressure field of any new configuration. At the end of the run, you’ll obtain the same output as your CFD solver, enabling you to visualize the geometries and flow field around the airfoil.
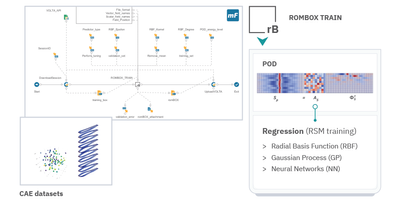
Enabling data governance and democratization for ROM with ESTECO VOLTA
A ROM model training can be automated, fine-tuned, and integrated into an automated design loop to make new design predictions faster. But if you want to really widen the use of ML data-driven modeling techniques, first you need to assimilate data within your organization and enable non-experts to re-use that data to seamlessly run ROM-based simulation evaluations.
Today, the majority of simulation data is assimilated by a handful of experts who have acquired experience over the years to make decisions at a very early stage of product development. In most cases, they work in silos. They generate specific data to build specialized surrogate models. If something needs to be modified based on new customer requirements, they will create a new surrogate model with a new set of data from scratch. In this scenario, how do you transfer and re-use the data from one project to another without a Simulation Process and Data Management (SPDM) framework in place? What if you could extend the use of ROM models towards designers and other stakeholders?
You can securely manage all the data associated with the simulation models and train ROM models using VOLTA, the digital engineering platform for SPDM and design optimization. The VOLTA platform allows your organization to collect and merge all the high-fidelity data in an authoritative source of truth that can be enriched by field experts. In this way, you can rationalize the management of all numerical models and exploit everything that has been evaluated before to train and validate ROM models. And these can be easily interrogated by non-experts from a simplified web interface. They can evaluate hundreds of new designs and check if they satisfy specific KPI or constraints in a fraction of seconds. VOLTA platform accommodates the needs of two types of users:
- ROM creator: a simulation expert or method developer who leverages the modeFRONTIER process automation and design optimization capabilities integrated in VOLTA to generate CAE datasets, train ROM models and make it consumable by others through an easy to use interface.
- ROM consumers: non-simulation experts like CAD designers who would perform ROM-based simulations by using a simplified application (already trained and validated by an expert) and make design predictions in real-time without the need for asking additional evaluation from CFD departments.
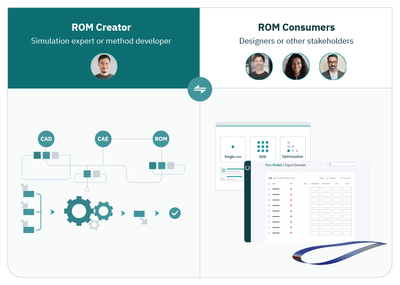
At its core, VOLTA provides your organization with data governance that harnesses the power of high-fidelity and low-fidelity data and enables a wider audience of engineers to make data-driven design predictions. With VOLTA’s web-based post-processing dashboards, you can analyze 3D ROM-based models and visualize scalar CAE results predictions and share insights in real-time with other stakeholders to make informed decisions.
In summary, with the introduction of Optimad's explainable AI (XAI) technology in modeFRONTIER and VOLTA software solutions we want to empower non-coding engineers to leverage advanced Machine Learning (ML) techniques. Our XAI technology allows you to move to a new data-driven paradigm, where physics-based simulation is used for DOE to enrich ML models with training datasets. These model can be re-used to run ROM-based simulations much faster while maintaining accuracy and interpretability of the relationships between variables and the physics underlying the models. Our approach is different because XAI technology is fully automated in the modeFRONTIER graphical workflow. XAI technology execution can be scaled in the VOLTA platform where non-simulation experts can simulate accurate designs in a fraction of time by seamlessly running design space exploration strategies on top of the ROM models. Whether ML is your organization's expertise or not, our team of experts will guide you through your ROM training journey from start to finish.
Get in touch with our experts and see how you can get instant design predictions with our XAI technology.
Interested in finding out more?
Get in touch with our experts and see how you can get instant design predictions with our XAI technology.
Interested in finding out more?
Get in touch with our experts and see how you can get instant design predictions with our XAI technology.