Optimizing offshore wind turbine monopile for hurricane-prone regions
Written by Matteo Bucchini and Gabriele Degrassi
19 April 2023 · 5 min read
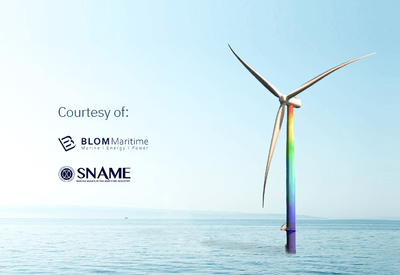
Offshore wind energy is developing rapidly in the United States. Several new wind farms, using turbines supported on fixed foundations, are at various stages of development, especially off the Northeast coast. Indeed, there are no plans for floating installations primarily because the continental shelf extends a considerable distance from shore and the waters are relatively shallow.
However, one of the key technical aspects to consider when designing offshore wind turbine monopile foundations is the presence of tropical cyclones on the U.S. East Coast. In hurricanes, maximum wind speeds can exceed the design limits of wind turbines, making them vulnerable. In addition to blade loss, the supporting monopile foundations can deform. To tackle this challenge, the goal is to design a wind turbine monopile system that functions when it is subjected to a critical load such as a strong storm.
Traditionally, the process of developing a design that meets these criteria is done iteratively relying on the project experience and skill of the engineers. Modern simulation and numerical analysis techniques have been developed to assist engineers in optimizing the design according to their set of criteria in less time. This is why we employed ESTECO’s modeFRONTIER process automation and design optimization software to demonstrate how the design of a monopile for a 15 MW turbine can be optimized to survive hurricane conditions.
Investigating the monopile structural design and response under environmental conditions
As with any large-scale investment in a project such as an offshore wind turbine farm, numerous factors need to be considered:
- Environmental (wind and marine conditions, seabed movement and scour, and other conditions such as air temperature, solar radiation, seismicity, maritime traffic, and so on)
- Structure (rotor-nacelle assembly, support structure, energy production and transfer, operation, maintenance, and emergency)
- Actions/loads (gravitational/inertial, aerodynamic, hydrodynamic, actuation, wake loads, impact loads, tsunami)
This project’s scope is limited to the structural design of a single wind turbine on a monopile foundation. For this study, we assumed as the starting point the NREL IEA 15-Megawatt Offshore Reference Wind turbine: the monopile has a diameter of 10 meters and is about 75 meters long; the monopile is circular in cross-sections; the wall thickness is the thickest segment and exceeds 55mm. Based on these considerations, we transformed the monopile design into a Finite Element (FE) model using ANSYS Workbench.
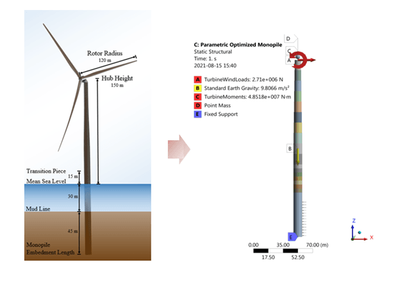
Structural design of a single wind turbine on a monopile foundation
Five connected Ansys Workbench blocks are the core of the analysis:
- Three static structural analysis blocks, in which loads, boundary conditions, and deformation-stress results are covered. Each of them covers one Load case.
- A modal analysis block, connected to the solution step of the previous block, which covers the natural frequencies extrapolation from the constrained geometry.
- Additionally, an Excel block is used to incorporate the sandy soil characteristics, which vary with the depth of the monopile. This block is linked to the Parameter set and gives information to the nonlinear springs, used to represent the soil behavior.
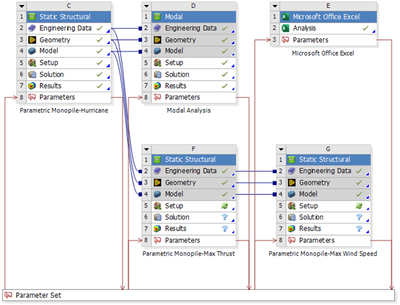
ANSYS Workbench for Finite Element Analysis (FEA)
With regards to the design loads, the monopile foundation is subject to the forces from the waves, currents, and wind turbine structure.. The wind turbine is designed to cut out at a given wind speed. During hurricane conditions, the blades are feathered to stop the turbine rotation and reduce the loads. The wind loads are calculated using OpenFAST NREL software under the following conditions:
- Wind speed from max thrust: 11m/s
- Max operational wind speed: 25m/s
- Hurricane condition: 50m/s
Design optimization process for a NREL 15 MW offshore wind turbine monopile model
The optimization-driven process was created and automated in modeFRONTIER workflow by integrating the Ansys FEA model and the openFAST NREL software to extract the loads from the operational conditions. The overall aim was to minimize the mass of the offshore wind turbine monopile. This is one of the most important parameters that influence the cost since it measures the amount of material used and the fabrication cost.
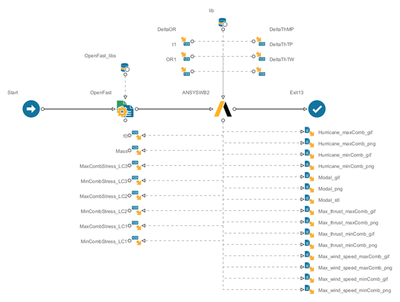
modeFRONTIER automated workflow for minimizing the mass of the offshore wind turbine monopile
Focusing on the overall structural geometry, the primary input design variables considered are the diameter of the monopile at the bottom and at the top of the tower, and the wall thickness discrete distribution along the height. The main output variables considered are the mass of the monopile, transition piece and tower, the maximum stress experienced, and the natural frequencies of the structure. Also, design constraints in this problem include maximum stress experienced in the monopile, buckling checks, and natural frequencies.
Once the simulation process workflow had been set up, we performed Design of Experiments (DOE) studies using the Uniform Latin Hypercube (ULH) algorithm from the modeFRONTIER Planner environment to create 42 configurations of the monopile. The aim was to minimize correlations between input variables and maximize the distance between generated designs to investigate which areas cover feasible designs before starting the optimization process.
A Sensitivity Analysis was carried out on the outcome of the DOE, highlighting an important influence of the t1 (thickness of the first section) and OR1 (outer radius of first section) parameters on all the outputs.
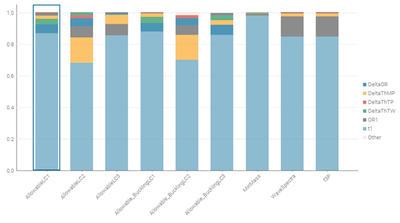
Effect chart of modeFRONTIER Sensitivity Analysis tool
Then, we applied the FAST RSM-based algorithm to run the design optimization study within modeFRONTIER. This allowed us to currently evaluate 202 designs, finding the best feasible design after 150 evaluations:
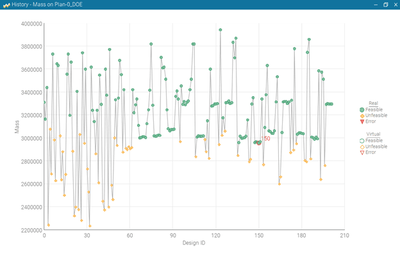
modeFRONTIER History chart: Mass value during optimization
Starting from the optimization results, the modeFRONTIER clustering tool was used to search for the best cluster and this subset was used as a starting point for a virtual optimization on a reduced design space.
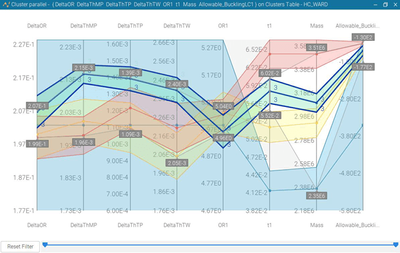
modeFRONTIER Cluster parallel coordinates chart: best cluster selected for virtual optimization
The process led to even better values of mass for three different designs, but once validated they proved to be in fact not better than the original best point.
Post process offshore wind turbine monopile model results in an SPDM framework for collaborative Design Optimization
To allow us to improve collaboration between the different subject matter experts involved in this project, the simulation results were then uploaded to the ESTECO VOLTA - an enterprise platform for Simulation Process and Data Management (SPDM) and Design Optimization. Thanks to the VOLTA Advisor, the advanced web-based data analysis environment, we could collaborate to compare and evaluate different wind turbine monopile design results in real time from an interactive dashboard.
VOLTA Advisor enables different Subject Matter Experts to collaboratively decide on the best design solution for the NREL 15 MW offshore wind turbine monopile
In summary, the reduction in mass for the multi case scenario is lower compared to the hurricane condition itself. The result is still significant. By including more loading conditions and design criteria, the results is an increased in the optimized mass value.
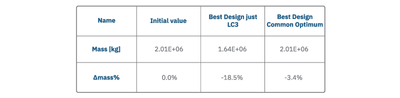
However, the weight of the structure has been reduced by more than three percent, with an associated reduction in the cost of construction. A note about the simulation workflow in the VOLTA SPDM platform: it’s impressive how powerful it is. We run hundreds of designs in half a day, finding the very best ones. And the VOLTA working environment gives you all the design exploration tools in the same place, available via browser from any computer. This is flexible and powerful at the same time.
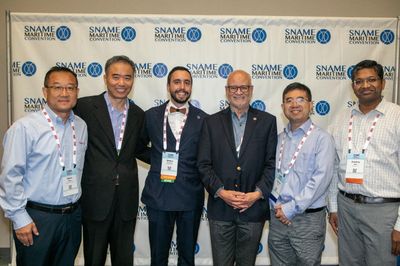
The research group at the SNAME Maritime Convention 2022 in Houston, US.
This research project has been undertaken by the HS-03 SNAME panel. These are the members and the supporting companies: Matteo Bucchini (BLOM Martine); Zhiyong Yang (7C Engineering); Roger I. Basu (Roger Basu & Associates); Aimin Wang (EXMAR Offshore Company)); Won Ho Lee (Lloyd’s Register); Gail Baxter (Consultant); Robert Sielski (Consultant); Raffaele Frontera (HMC BV); Gabriele Degrassi (ESTECO). Recently, the HS-03 panel also participated to a technical discussion/workshop "Expanding Engineering Knowledge for Floating Offshore Wind" organized in partnership with the University of New Orleans and the Louisiana Wind Energy Hub at UNO.
modeFRONTIER is the leading software solution for simulation process automation and design optimization
Design better products faster
modeFRONTIER is the leading software solution for simulation process automation and design optimization
Design better products faster
modeFRONTIER is the leading software solution for simulation process automation and design optimization