Design innovative products faster with integration and process automation in Computational Fluid Dynamics (CFD)
Written by Simone Genovese
8 June 2021 · 6 min read
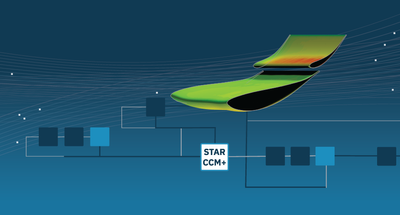
Competing in today's global scene, developing products that stand out is every day more challenging. According to a research conducted by Tech-Clarity manufacturing companies rely on the increased quality, high performance, and more significant innovation at a lower cost to differentiate their products and beat the competition.
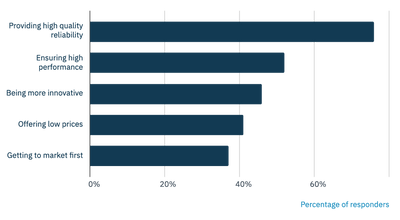
In this pursuit, engineering teams report that they dedicate half of the time in innovation and design activities while a third is spent on non-value-added work.
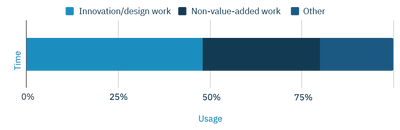
Based on our 20+ years of experience in the process automation and design optimization field, at ESTECO we know there’s room for improvement, not only in the menial work but also in the design area. Indeed, this kind of work often includes repetitive activities, a lot of trial-and-error methods, and the use of independent tools to achieve a satisfactory solution.
Using CAE (Computer-Aided Engineering) as a core technology from very early in the design process to the final verification phases of production helps reduce idle time and outperforms manual work.
Formalizing this manual work, through an easy-to-read modeling notation, provides several acknowledged benefits. It allows automating the design process giving engineers time to concentrate on important design aspects, while calculations are performed autonomously night and day. Even more importantly, formalizing the process once allows engineering teams to reuse best practices in future projects and share them inside the company.
One of the pillar disciplines to improve product designs and rapidly develop viable virtual prototypes is CFD (Computational fluid dynamics).
CFD techniques offer different advantages compared to experimental methods: detailed information about flows, deep product performance understanding, and reduction in testing cost to name a few. They do not require any large capital facility and allow investigation where experimentation is not possible.
CFD and Optimization-Driven design: coupling modeFRONTIER and Star-CCM+
modeFRONTIER, the design optimization and process automation software developed by ESTECO, guarantees the management of all logical steps of an engineering design process. It enables the automation of any parametric simulation process by integrating in a single workflow any third-party tool, including CFD solvers.
The available interfaces include Star-CCM+, the most used CFD software in the market, according to a recent survey of Resolved Analytics. Star-CCM+ provides the most comprehensive engineering multi‑physics simulation inside a single integrated package, including:
- Fluid dynamics, solid mechanics, fluid-structure interaction, heat transfer, and many other.
- Replication of rigid and flexible body motions with techniques including mesh morphing, overset mesh, and six degrees of freedom (6DOF) motion.
However, managing Fluid Dynamics Simulations is not enough to produce competitive products. At least two more factors need to be kept into account:
- Iteratively design and update the physical system's geometry that needs to be approximated by a geometric CAD type model.
- Adequate calculation infrastructure (HPC) to support the CFD workload, from complex fluid flows involving turbulence to acoustics and electromagnetics.
The capabilities of modeFRONTIER for Process Automation, Distributed Execution and Design Optimization fit the bill, managing all the engineering design process's logical steps. Its suite of direct interfaces with the most popular engineering solvers, now includes Star-CCM+.
The modeFRONTIER direct interface to Star-CCM+ seamlessly connects with simulation models, extracts relevant parameters and allows to select process inputs and outputs in a few clicks through a simple guided process. Add constraints and objectives, and you are all set to run your process and exploit the benefits of process automation.
To better explain the true potential of the coupling, let’s see a generative design approach with a simple use case using modeFRONTIER and Star-CCM+.
Generative design is an iterative design process that uses CFD to generate a certain number of designs and meet certain constraints. An optimizer then fine-tunes the feasible region by selecting specific designs or changing input values, ranges, and distribution to match the desired objectives.
Optimizing the design of an idealized water-cooled car radiator
When it comes to sizing the radiator in the function of car specifications, many variables come into play. Size and geometry of the radiator, materials, coolant composition, and many others. Each of these parameters is not independent, and the final goal usually is to find the smallest/lightest possible radiator capable of reducing the liquid temperature to safe values.
modeFRONTIER allows optimizing the geometry and fluid-dynamics parameters concurrently with a holistic perspective of the system, even integrating different tools. Through the parameter chooser, a tool available inside the software, it’s easy to parametrize the Star-CCM+ model and automate the configuration of boundary conditions for the inlet and outlet of the water, such as temperature, mass flow rate, and all the parameters depending on the concentrations of the fluids we want to evaluate.
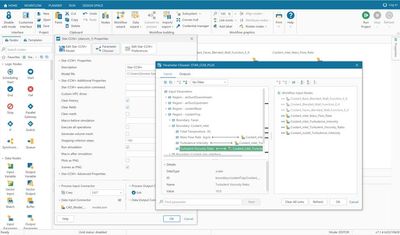
modeFRONTIER Parameter Chooser
Within the workflow, modeFRONTIER machine learning algorithms autonomously generate high-performing design alternatives with optimized geometry often providing solutions far removed from a traditional design.
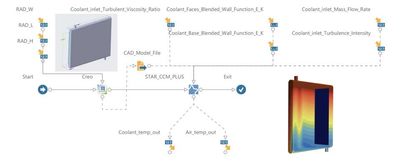
modeFRONTIER workflow
Thanks to the new integration the time required to define the process is dramatically reduced and no development skills are required.
In addition to that, once the workflow and the strategy are defined, modeFRONTIER is able to parallelize the execution on your HCP exploring all the possible solutions in a fraction of the time usually required to manually evaluate all the interesting designs.
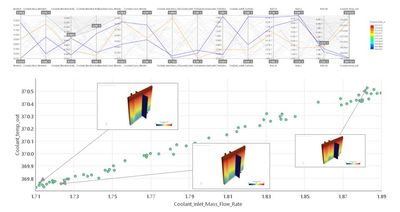
modeFRONTIER charts
Exploiting High-Performance Computing (HPC) with CFD techniques
The use of modeFRONTIER scalability on HPC helps even further exploiting CFD techniques.
As a matter of fact, CFD grew hand-in-hand with modern supercomputers, as an increasing calculation power is necessary to solve the complex CFD equations (such as very high-speed flow simulation) that otherwise would require computation months.
The equations involved in fluid dynamics are Navier–Stokes equations. Navier-Stokes equations are nonlinear partial differential equations, and except for some very specific cases, it’s very difficult if not impossible to find an analytical solution to them. Still, it is possible to obtain an approximate solution using a discretization method that approximates the partial differential equations by a set of algebraic equations. Thus, CFD is the process of converting the partial differential equations of fluid dynamics into simple algebraic equations, which relate to small sub-volumes within the flow, and then solving them numerically to obtain some meaningful result.
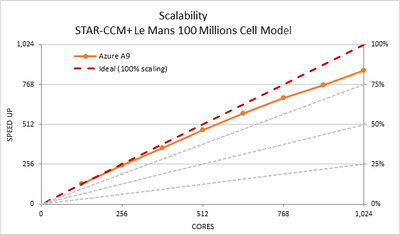
Scalability of STAR-CCM+ on Microsoft Azure using the “Le Mans 100 million cell” test model. (Image courtesy of Microsoft Azure.)
modeFRONTIER 2021R2 Release allows driving Star-CCM+, simplifying the process automation creation, eliminating the burden of developing a custom JAVA macro for each Star-CCM+ model, and allowing exploitation of company computing resources.