BASF Catalysts solutions meet exhaust emissions standards with modeFRONTIER
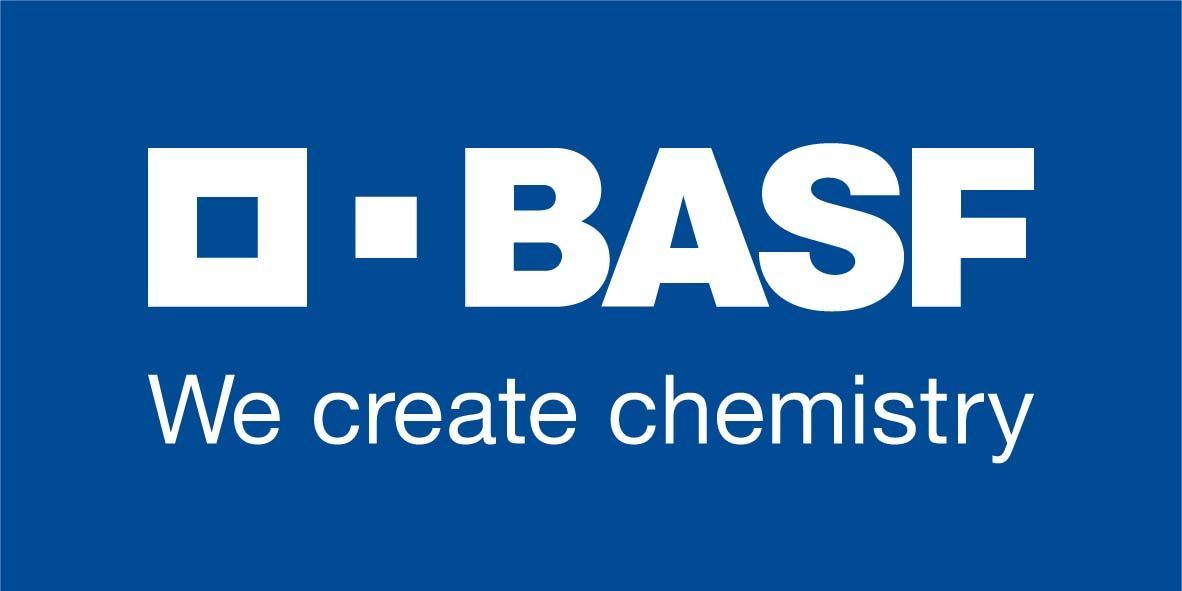
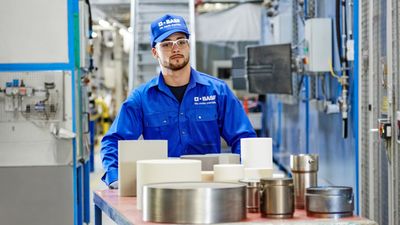
- Company: BASF
- ESTECO Software Solution: modeFRONTIER
- Benefits:Evaluate 500 catalyst system designs within two weeksIdentify the suitable prototype candidates capable to exactly match particular cost and performance targets based on customer preferencesSave catalyst and test costs and minimize exhaust emissions
Using modeFRONTIER to optimize exhaust aftertreatment systems
BASF’s Catalysts division is the world’s leading supplier of environmental and process catalysts. Responding to a request from a customer - a truck manufacturer - BASF researched to provide an alternative technology capable of reducing catalysts costs and improving the performance of the current Euro VI production exhaust aftertreatment system. BASF proprietary exhaust simulation models were integrated in modeFRONTIER software, with the aim of optimizing the operational parameters for accurate emissions prediction.
"Our simulation toolchain combined with modeFRONTIER optimization capabilities led to evaluate 500 catalyst system designs within two weeks. Manufacturing and testing few prototypes would have taken us months and significant resources due to the expensive precious metals incorporated and additional operational costs."
Challenge
The global automotive industry faces enormous challenges from increasingly tightening emissions legislations. Regulatory differences between European, Asian and American markets enhance complexity while vehicle manufacturers are constantly seeking to reduce development cycle times. There is a continuous demand for efficient strategies to develop cost effective solutions that meet regional emissions regulations. As a result, simulation techniques for exhaust aftertreatment system has gained popularity. Engineers at BASF focused on developing a model-based simulation for an exhaust system comprising a diesel oxidation catalyst in order to investigate the trade-off between cost and catalytic performance. Besides the minimization of the tailpipe NOx emissions by simulating a transient homologation cycle (WHTC), several functionalities of the oxidation catalyst like NO and hydrocarbon oxidation needed to be optimized in parallel.
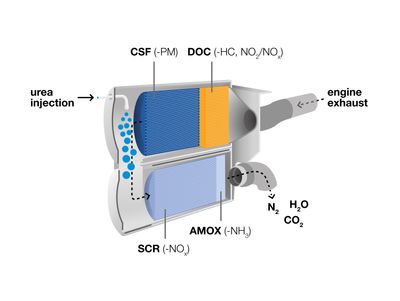
Scheme of Euro VI exhaust aftertreatment system.
Solution
An effective model based development toolchain was developed building upon BASF proprietary exhaust catalyst models to simulate accurate emissions prediction. Four catalyst design parameters, considered as major cost drivers, were investigated in modeFRONTIER multiobjective optimization platform. As a first step, performing Design of Experiments (DOE) analysis allowed to identify the most important parameters and explore sensitivity of the system performance. Consequently, the optimization task was driven by the MOGA-II, the genetic algorithm included in modeFRONTIER, to minimize catalyst cost and tailpipe emissions.
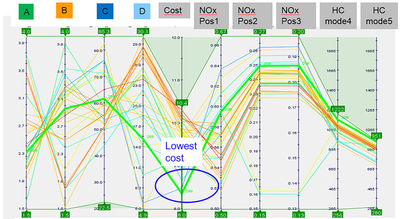
Parallel coordinate chart allows selection of desired cost and system performance.
Benefits
“Our simulation toolchain combined with modeFRONTIER optimization capabilities led to evaluate 500 catalyst system designs within two weeks. Manufacturing and testing few prototypes would have taken us months and significant resources due to the expensive precious metals incorporated and additional operational costs. Despite the large amount of data, modeFRONTIER allowed to quickly rationalize and visualize results in a smart and efficient way. The Parallel Coordinate Chart enabled us to identify the suitable prototype candidates capable to exactly match particular cost and performance targets based on customer preferences. We look forward to demonstrating the benefits of the toolchain for other customer applications” said Dr. Stefan Kah, responsible for Application Engineering Modeling at BASF Catalysts Germany GmbH.
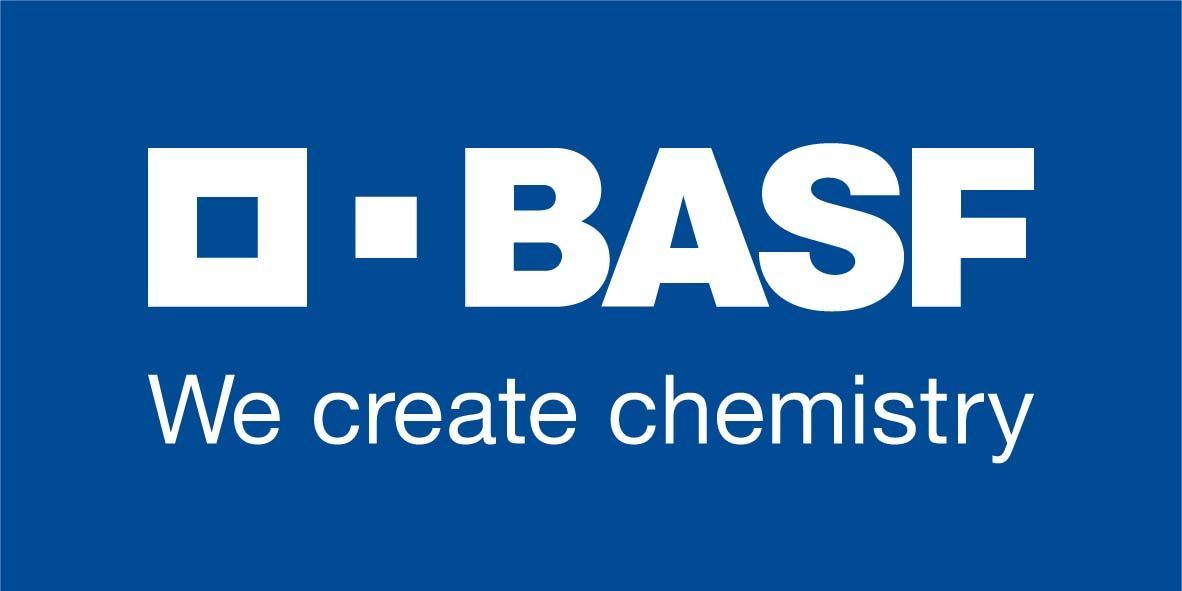
BASF’s Catalysts division is the world’s leading supplier of environmental and process catalysts. The group offers exceptional expertise in the development of technologies that protect the air we breathe, produce the fuels that power our world and ensure efficient production of a wide variety of chemicals, plastics and other products, including advanced battery materials. By leveraging our industry-leading R&D platforms, passion for innovation and deep knowledge of precious and base metals, BASF’s Catalysts division develops unique, proprietary solutions that drive customer success. catalysts.basf.com