modeFRONTIER helps Cummins Improve Engine Performance
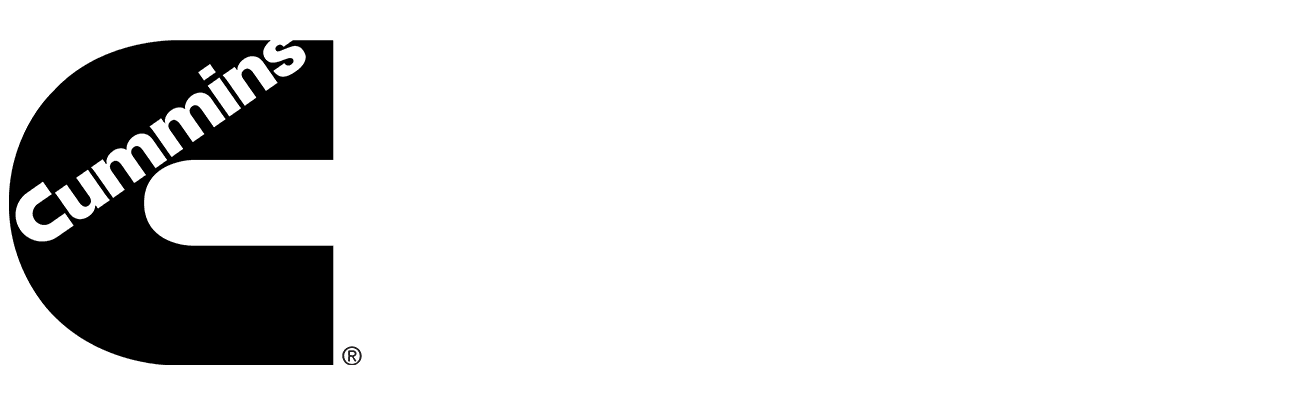
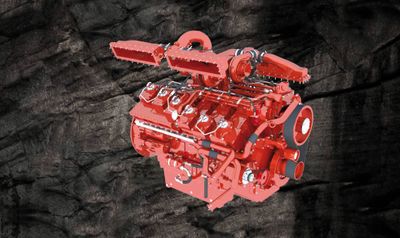
- Company: Cummins
- ESTECO Software Solution: modeFRONTIER
- Benefits:Reduce design cycle time, improving the performance of the valve train systemFind the optimal valve timing configuration with a two-step processAutomate the calibration process
Using modeFRONTIER to integrate GT-Valve train and GT-Power models for valve event optimization
Cummins Engine, a leader in the manufacturing of diesel and natural gas-powered engines for a wide range of transportation and equipment purposes, has created a new power module ready to take on the stringent US - EPA regulations. It is significantly more compact and cost-effective than medium-speed engines at the same horsepower. It took 150 engineers to design it, and modeFRONTIER helped the High Horsepower group find the optimal valve timing, hence reducing fuel consumption.
"modeFRONTIER helped drastically reduce the time taken for calibrating GT models."
Challenge
When designing piston engines, timing when opening and closing inlet and exhaust valves is a crucial parameter impacting the fuel consumption / power output ratio. Typically, delaying the Exhaust Valve Closing (EVC) and anticipating the Intake Valve Opening reduces Exhaust Gas Residuals, resulting in lower fuel consumption. Among the complex models composing the 16-cylinder engine, Cummins designers used GT-Suite (Valve Train and Power modules) to simulate valve event performance and dynamics. For optimal engine performance, valve timing and lift profile need to be perfected for given breathing configurations defined by engine speed, and valve and port geometry and performance.
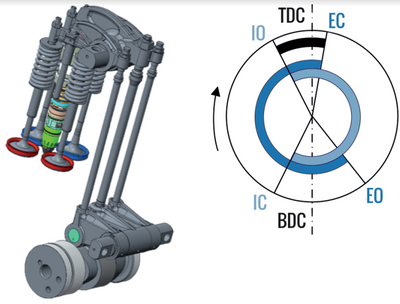
Valve train components.
Solution
Finding the optimal valve timing configuration required a two-step process; to start, a first workflow was created in mode FRONTIER and used to automate the calibration process. Valve train parameters were automatically adjusted with modeFRONTIER to calibrate the GT model and match measured push tube load. The second phase consisted in a second workflow, which was used to investigate the design space; initially with response surfaces and subsequently with the direct optimization algorithms NSGA and Hybrid - to find the best values for 12 output parameters measuring the exhaust and intake cam timing angles, the volumetric efficiency and the Brake Specific Fuel Consumption (BSFC)1.
Benefits
During both project phases, modeFRONTIER proved highly reliable for reducing design cycle time and improving the performance of the valve train system. From the outset “it helped drastically reduce the time taken for calibrating GT models” said Ambikapathy Naganathan (Structural and Dynamics Analysis Engineer at Cummins). “modeFRONTIER has an excellent capability for integrating with multiple GT models and post processing tools.” Continued Eng. Naganathan: “in fact it helped us link those GT models more efficiently and complement the in-house optimization tool, while at the same time maintaining concurrent use by different analysts in different locations.”
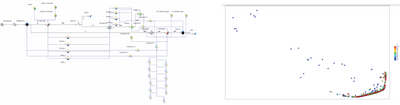
Valve event optimization workflow with Hybrid algorithm and Pareto Front (HYBRID Algorithm).
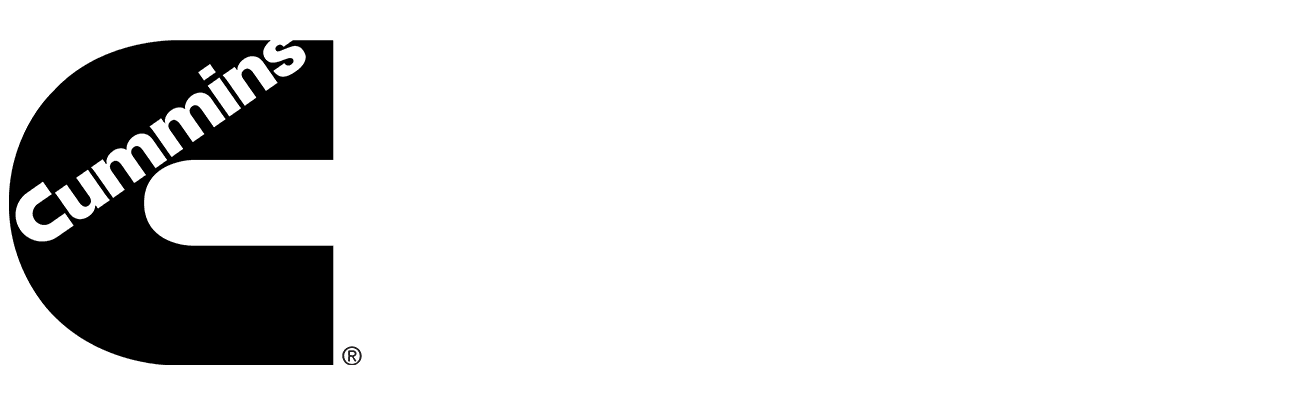
Cummins Inc., a global power leader, is a corporation of complementary business units that design, manufacture, distribute and service engines and related technologies, including fuel systems, controls, air handling, filtration, emission solutions and electrical power generation systems. Cummins serves customers in 190 countries and territories through a network of more than 600 company-owned and independent distributor locations and approximately 6,500 dealer locations. cummins.com